Új lehetőségek a roncsolásmentes vizsgálati technikában
///////////////////////////////////////////////////////
Dr. Czinege Imre
egyetemi tanár
Széchenyi István Egyetem
Csizmazia Ferencné Dr.
főiskolai docens
Széchenyi István Egyetem
Kozma István
egyetemi tanársegéd
Széchenyi István Egyetem
/////////////////////////////////////////////////////
Az optikai digitális képalkotás és képelemzés a roncsolásmentes anyagvizsgálatban egyre gyakrabban alkalmazott technika. Segítségével a mikroszkópos és sztereo mikroszkópos felvételek, endoszkópos képek, repedésvizsgálatokkal kimutatott felületi hibák, felületi topológiai jellemzők, klasszikus ultrahangos és röntgen vizsgálati jelek értékelése automatikusan, szubjektív hibáktól mentesen megoldható. Ebből a gazdag kínálatból két témakörre fókuszál a jelen publikáció: a három dimenziós képalkotást megvalósító ipari komputer tomográfiára (CT), valamint a felületi topológia térbeli ábrázolására és mérésére alkalmas fénymikroszkópra és konfokális lézer mikroszkópra. Mindkét eljárás közös jellemzője az, hogy valós térbeli képet ad, amely kép a korszerű vizualizáló és elemző szoftverekkel sokoldalúan jellemezhető.
Az ipari komputer tomográf működési elve
A komputer tomográf segítségével összetett külső és belső geometriák ellenőrizhetők nagy pontossággal, a síkbeli röntgen felvételeknél lényegesen gazdagabb információ nyerhető a belső hibákról és a felbontástól függően az anyag szerkezetéről is, mindezt gyorsan és roncsolásmentesen kapja kézhez az anyagvizsgáló szakember. A térfogati anyaghibákat (üregek, zárványok) a kiértékelő rendszer automatikusan detektálja. Ezek a hibák mind a 3D-s geometrián, mind a 2D-s metszeten vizualizálhatók. További előnye a technikának, hogy komplex, több anyagból és alkatrészből álló szerkezetek felépítése, esetleges hibái is ellenőrizhetők, az egyes alkatrészek és azok kapcsolata a szerkezetből kiemelten is megjeleníthető. Az ipari CT az orvosi diagnosztikai eszközhöz hasonlóan 2D-s röntgen felvétel sorozatot készít a vizsgálandó objektumról úgy, hogy a tárgyasztal és az azon felfekvő alkatrész egy kis szöggel sorozatosan elfordul. Ez addig ismétlődik, amíg az alkatrész teljesen körbe nem ér és ez idő alatt minden egyes szögelforduláskor egy röntgenkép készül. A munkadarab ellentétes oldalán elhelyezett sík vagy vonal detektor érzékeli az intenzitás változást. Az 1. ábra a vizsgálati elrendezést mutatja.
Az a.) ábra hasonlít a klasszikus röntgen technikához azzal a különbséggel, hogy nem egyetlen 2D-s átvilágítás készül az alkatrészről, hanem a tárgy minden egyes kis szögelfordulásakor egy röntgenképet tárol a készülék. A b.) ábrán vonaldetektor érzékeli az intenzitás különbségeket, ennél a vizsgálatnál a röntgencső és a vonaldetektor együtt mozog függőlegesen, és közelítően milliméterenként készül egy szelet a forgó tárgyról. Emiatt a vizsgálat hosszadalmas, például egy hengerfej leképezése több óráig is eltarthat, ugyanakkor az így kapott kép élessége jobb, mint a síkdetektorral felvett képé. Mindkét leképezési mód esetében a mért jelek feldolgozását és sokoldalú elemzését hatékony 3D szoftver segíti. A Széchenyi István Egyetem Anyagismereti és Járműgyártási Tanszékén 2010 júniusa óta üzemel egy YXLON Y.CT Modular ipar CT berendezés. A gép különlegess
ége, hogy 2 röntgensugár csővel és két detektorral van felszerelve. A kisebb csőfeszültségű (225 kV) mikrofókuszú röntgencsővel akár a 7µm-es, a nagyobb feszültségű csővel (450 kV) pedig 50 µm-es felbontás érhető el. Az átvilágítható falvastagság acélok esetén 70 mm, alumínium ötvözeteknél 120 mm. A berendezés 7 manipulátorral működő portál rendszerével 800 x 1200-as kubatúrájú alkatrészek vizsgálhatóak. A gép vizsgálati lehetőségei széleskörűek, használható 3D geometriai rekonstrukcióra, inhomogenitás vizsgálatra (porozitás, zárványok, fogyási üregek), falvastagság és egyéb geometriai jellemzők mérésére, Ezen funkciók minőségbiztosítási és kutatási célokra egyaránt alkalmassá teszik. Tárgyasztal és az azon felfekvő alkatrész egy kis szöggel sorozatosan elfordul. Ez addig ismétlődik, amíg az alkatrész teljesen körbe nem ér és ez idő alatt minden egyes szögelforduláskor egy röntgenkép készül. A munkadarab ellentétes oldalán elhelyezett sík vagy vonal detektor érzékeli az intenzitás változást. Az 1. ábra a vizsgálati elrendezést mutatja. Az a.) ábra hasonlít a klasszikus röntgen technikához azzal a különbséggel, hogy nem egyetlen 2D-s átvilágítás készül az alkatrészről, hanem a tárgy minden egyes kis szögelfordulásakor egy röntgenképet tárol a készülék. A b.) ábrán vonaldetektor érzékeli az intenzitás különbségeket, ennél a vizsgálatnál a röntgencső és a vonaldetektor együtt mozog függőlegesen, és közelítően milliméterenként készül egy szelet a forgó tárgyról. Emiatt a vizsgálat hosszadalmas, például egy hengerfej leképezése több óráig is eltarthat, ugyanakkor az így kapott kép élessége jobb, mint a síkdetektorral felvett képé. Mindkét leképezési mód esetében a mért jelek feldolgozását és sokoldalú elemzését hatékony 3D szoftver segíti. A Széchenyi István Egyetem Anyagismereti és Járműgyártási Tanszékén 2010 júniusa óta üzemel egy YXLON Y.CT Modular ipar CT berendezés. A gép különlegessége, hogy 2 röntgensugár csővel és két detektorral van felszerelve. A kisebb csőfeszültségű (225 kV) mikrofókuszú röntgencsővel akár a 7µm-es, a nagyobb feszültségű csővel (450 kV) pedig 50 µm-es felbontás érhető el. Az átvilágítható falvastagság acélok esetén 70 mm, alumínium ötvözeteknél 120 mm. A berendezés 7 manipulátorral működő portál rendszerével 800 x 1200-as kubatúrájú alkatrészek vizsgálhatóak. A gép vizsgálati lehetőségei széleskörűek, használható 3D geometriai rekonstrukcióra, inhomogenitás vizsgálatra (porozitás, zárványok, fogyási üregek), falvastagság és egyéb geometriai jellemzők mérésére, Ezen funkciók minőségbiztosítási és kutatási célokra egyaránt alkalmassá teszik.
A CT-vizsgálat alkalmazási területei, vizsgálati tapasztalatok
Az elmúlt időszakban sokféle vizsgálati igénnyel jelentkeztek a környező járműipari és egyéb alkatrész beszállító vállalkozások. Jelentős volt az érdeklődés alumínium öntvények belső hibáinak kimutatására és komplex szerkezetek elemzésére. A további példák az itt szerzett tapasztalatokat mutatják be.
Alumínium öntvények vizsgálata
Féknyereg komplex ellenőrzése:
A 2. ábrán látható alkatrész térbeli felvétele jól mutatja a belső üregek elhelyezkedését, emellett az értékelő szoftver eltérő színekkel mutatja az automatikusan detektált hibák méretét (választható térfogati és hossz méret is). Egy tetszőleges metszeten is bemutathatók a hibák, és azokról táblázatos adatok is kérhetők, ahol megjelenik a hiba helye és fő méretei. Mód van egyes pórusok mérésére és ábrázolására is.
Vízpumpa ház vizsgálata
E vizsgálat beszállítói minőség-ellenőrzés céljából készült, ugyanis esetenként szivárgás volt tapasztalható a szerkezetben. A különböző metszetekről bemutatott képek jól illusztrálják az észlelt hibákat, amelyekből a szivárgás útjára lehetett következtetni.
Hengerfej geometriai méreteinek ellenőrzése
E vizsgálat célja a széria indításakor kötelező mesterdarab ellenőrzés volt. Korábban a vizsgálatot két részre bontva lehetett elvégezni, a külső geometriai méreteket a GOM digitális optikai mérőrendszerrel végezte az Egyetem, a belső hibák detektálására pedig klasszikus röntgen felvételek készültek. A CT vizsgálat mindkét vizsgálat elvégzésére alkalmas azzal a többlettel, hogy ily módon az öntvény belsejében lévő geometriai méretek is ellenőrizhetők, ahogy a 4. ábra jobb oldali képe mutatja.
Komplex szerkezeti egységek elemzése
Szerelt és forrasztott olajhűtő vizsgálata
Az 5. ábrán látható olajhűtőt rétegenként szerelik össze, majd speciális forrasztási technológiával egyesítik. A vizsgálat célja az volt, hogy egy ilyen komplex szerkezeti egységről egyáltalán milyen információk nyerhetők, lehet-e észlelni az esetleges forrasztási hibákat vagy geometriai eltéréseket? A vizsgálatok azt mutatták, hogy a térbeli geometrián sokoldalúan szemléltethetők az egyes részletek, és detektálhatók a kérdéses eltérések.
Katalizátor vizsgálata
Ez a vizsgálat egy hosszabb ideig üzemelő katalizátor lerakódásainak, por szennyeződéseinek detektálására irányult. A megbízó szerint ezeket a változásokat eddig csak roncsolásos úton lehetett vizsgálni, mert a hagyományos röntgen felvételek nem mutatták ki a változásokat. Az ábra tanúsága szerint a CT-felvételen kitűnően tanulmányozható a katalizátor szerkezete, és a metszeteken jól láthatók a keresett lerakódások.
Termosztát szerkezet fárasztása
A 7. ábrán látható termosztát a jármű motorra felszerelve esetenként hibás jelzéseket továbbított a vezérlés felé. A helytelenül működő egységek vizsgálata a termosztát érzékelő villamos kontaktusának megszakadását mutatta. A magas hőmérsékleten végzett ciklikus rázó vizsgálat közben a villamos érintkezés megszűnését lehetett detektálni, de a termosztát belsejében bekövetkezett vezeték szakadás helyét csak roncsolásos vizsgálattal lehetett megállapítani. A műszer beérkezése után elvégzett CT-vizsgálattal a hagyományos gondolkodásmódtól teljesen eltérő, új lehetőségek tárultak fel azzal, hogy az összetett, különböző anyagú alkatrészekből álló szerkezet tökéletesen megjeleníthető volt térbeli ábrán, az egyes alkatrészek külön kiemelhetők és elemezhetők voltak. Ezáltal szerkezet fárasztás közben az egyes komponensek elhasználódása az idő függvényében kitűnően tanulmányozhatóvá válik, ha ugyanazt az egységet különböző igénybevételi számok után kiemelve vizsgáljuk, majd tovább fárasztjuk.
Árammérő szonda vizsgálata
Az árammérő szonda vizsgálati igénye hasonló volt a termosztátéhoz. Itt azt kellett megállapítani, hogy a tekercs stabilizálása érdekében a tekercs és a ház közé beöntött műgyanta vastagsága, ezáltal a tekercs helyzete megfelelő-e? A 3D felvételek ezeket az eltéréseket jól kimutatták.
Kompozit vízpumpa ház vizsgálata
Egyes szállítóktól származó vízpumpa házakon repedés jelent meg, a feladat az ok kiderítése volt. Hipotézisként kínálkozott, hogy az erősítő karbon szálak nem megfelelő eloszlása okozza a hibát. A probléma megoldását két irányból közelítettük: Moldflow szimulációval elemeztük a szálak várható elrendeződését, CT-felvételekkel pedig a repedés környezetének vizsgálatára került sor. A CT vizsgálat kimutatta, hogy a repedés alatti térben a karbon szálak rendezetlenül helyezkednek el és a fröccsöntés során üregek keletkeztek. A hiba a meglövési pont változtatásával korrigálható.
A CT és hagyományos röntgen technika összehasonlítása
Mindkét eljárásnak megvannak az előnyei és hátrányai, a vizsgálati cél dönti el, hogy mikor melyiket célszerű alkalmazni. Az alábbi táblázat mutatja az összehasonlítást:
CT röntgen berendezés |
Hagyományos ipari röntgen |
• Teljes 3D képalkotás • Hiba méret és koordináta • CAD modell alkotás • Bármilyen külső v. belső méret megmérhető
|
• Egy vetítési irányból 2D kép • Hiba méretek vetületben láthatók • Csak vetített kép látható • Méretek korlátozottan láthatók, becsülhetők
|
• A berendezés ára magas • A felvétel ideje több óra is lehet • Csak laboratóriumi vizsgálatra alkalmas
|
• A berendezés ára elfogadható • Gyors felvétel készítés • Helyszíni vizsgálat terjedelmes szerkezeteken lehetséges
|
Felület topológiai vizsgálatok fénymikroszkóppal és konfokális lézer mikroszkóppal
Optikai mikroszkópos vizsgálatoknál közismert az, hogy egy görbült felületnek egyszerre csak egyes részletei élesek, de a fókusztávolság változtatásával más rétegek is élessé tehetők. Ha tehát a mikroszkóp célszerűen választott lépés távolsággal változtatja a lencse és az objektum közötti távolságot, és az így felvett éles részleteket térbeli képpé egyesíti, akkor olyan felvétel kompozíció jön létre, amelyhez z-irányú méretek rendelhetők. Ezáltal a hagyományos optikai mikroszkóp az értékelő szoftver segítségével valós térbeli képet ad a felületről, amelyből nagyon sok információ nyerhető. A magassági eltéréseket a szintvonalakhoz rendelt színekkel lehet megjeleníteni, tetszőleges metszetről profilogram vehető fel, amellyel karcok szélessége és mélysége mérhető meg, és a felület kollektív tulajdonságai, például az átlagos érdesség vagy az érdesség magasság is meghatározható. Ugyanezek a mérési lehetőségek adódnak a konfokális lézer mikroszkóp alkalmazásával is, de az előbbinél lényegesen nagyobb felbontásban. A leképezés elvét a 10. ábra mutatja. A bal oldali kép a különböző élességű felvétel sorozatot mutatja, amelyet a képen látható „z” távolság felosztásával állít elő a mikroszkóp. A berajzolt sugármenetek jelzik a különböző fókusztávolságokat. A jobb oldali kép azt mutatja, hogyan pásztázza le a lézersugár a látómezőt. Megjegyzendő, hogy a mikroszkóp asztal x-y irányú mozgatásával egy felületről több látómező is felvehető automatikusan, ezek a mozaik képek, amelyekből a szoftver egységes képet hoz létre. A topológiai mérésekre alkalmas mikroszkópok a pásztázó elektronmikroszkóp hasznos kiegészítői lehetnek azzal az előnyös tulajdonságukkal, hogy a szkenning képek gazdag információ tartalmát a z-irányú mérési lehetőséggel egészítik ki. A továbbiakban a mérési lehetőségek összehasonlítását mutatjuk be.
A 11. ábrán látható képek gömbgrafitos öntöttvasból készült főtengely löketcsapjának szuperfiniselt felületét mutatják. A pásztázó elektronmikroszkópos képen jól látható egy éles karc, de annak mélységéről nem ad információt a felvétel. A lézer mikroszkópos felvételen jól látható a térbeli képen kijelölt metszősík, az alsó képen pedig a profil magasság változása. A 12. ábra a hipereutektikus alumínium-szilícium ötvözetből készült motorblokkok felületét mutatja megmunkált állapotban. A felület kezelési technológia lényege az, hogy hónolás után a primer szilícium kristályok körül elhelyezkedő lágyabb eutektikumot mechanikus vagy vegyi kezeléssel mélyítik, ezáltal a futófelületet a nagy keménységű primer szilícium krisztallitok alkotják. A bal oldali kép a pásztázó elektronmikroszkópos felvételt mutatja, ahol a Si krisztallitok jól azonosíthatók, és síkbeli méreteik is meghatározhatók. A jobb oldali kép ugyanezen felület EDS elemzéssel felvett képét mutatja, ahol szintén jól kiemelkednek a Si krisztallitok. A 13. ábra ugyanennek a felületnek egy másik részletét mutatja konfokális lézer mikroszkópos felvételen. A szilícium krisztalliton áthaladó metszősík definiál egy felületi profilgörbét, amelyen tetszőleges pontok jelölhetők ki a magasság irányú méretek jellemzésére. A piros jelölő vonal a Si-krisztallit platóját, a kék jelölő vonal az eutektikum mélypontját jelöli. A kettő közötti magasságkülönbség 2,4 μm, amely reális érték. Összehasonlításként megvizsgáltuk a felületet Talisurf CL200 típusú profilmérővel is. A színezett topológiai képet és a letapogatott térbeli alakzatot a 14. ábra mutatja. Látható, hogy a tűs letapogatás miatt a felület kissé más képet mutat, mint a konfokális mikroszkópos felvételen, de jellegük hasonló, és a z irányú méretkülönbség is 2,5 μm körüli értékre adódik. A bemutatott felvételek egymást megerősítik a topológiai rajzolat és a mért magasságkülönbségek tekintetében. A konfokális lézer mikroszkóp legnagyobb előnye a letapogatással szemben az, hogy lényegesen gyorsabban eredményt ad, és a felületet valósághoz közelibb módon képezi le, ugyanis a tű geometriájából adódó torzulások nem jelentkeznek. Egy másik érdekes felvétel sort mutat a 15. ábra, amely öntöttvas blokk lézerrel kezelt futófelületéről készült. A grafit lemez legmélyebb pontja és a lemez peremén lévő enyhe dudor magassága közötti különbség 1,4 μm, ez a mérés korábban semmilyen mikroszkópos technikával nem volt elvégezhető. Ugyanezen ábra jobb oldali képe a felület 3D ábrázolását mutatja. A mért értékek hitelességét érdességi etalonon végzett ellenőrzéssel valósítottuk meg. Az Rz=9 μm-es etalon csúcsmagassága a méréskor ugyanerre az értékre adódott. Mindezek a vizsgálatok igazolják, hogy a konfokális lézer mikroszkópos felvételek jól kiegészítik a pásztázó elektronmikroszkópos vizsgálatokat.
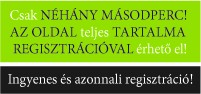
Ajánló
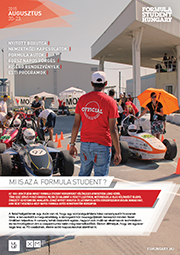
Autótechnika
- A JÖVÕ MOBILITÁSA ELÕADÁSSOROZAT
- Suttogó fékbetétek: Akusztikai tesztek a fokozott fékezési
- VÁSÁRIDÕ